「必要なものを、必要なときに、必要な数だけつくる」という発想から生まれたジャストインタイム(JIT)。もともと製造関係の企業で使われてきた生産管理システムです。最近では製造業界だけでなく、あらゆる分野で応用的に取り入れられています。
ジャストインタイムの概念や仕組み、活用方法などについて解説しましょう。
目次
1.ジャストインタイム(Just In Time)とは?
「ジャストインタイム」とは、トヨタ自動車が開発した生産管理のシステムのこと。「必要なものを、必要なときに、必要なだけ」供給するための生産計画という考え方を原型としています。
自動車のように何万種類もの部品が必要な製品を扱う工場では、効率のよい生産が必要です。その中、部品を効率よく仕入れ、大量生産を可能にし、
- ムダ
- ムラ
- ムリ
を防ぐことができる管理方法として知られています。
トヨタ生産方式とは?
トヨタ自動車独自の生産方法は、徹底的に無駄を排除し、製造工程の合理性を求めるもの。今では多くの企業がこの生産方法にならった体制をつくるようになりました。
トヨタ自動車のシステムは、
- 自働化:生産性をアップさせる生産工程
- ジャストインタイム:無駄をなくし生産効率をアップさせる
2つの考え方を大きな柱としています。
①自働化
「自働化」はトヨタ自動車の創業者、豊田佐吉氏が発明した織物の機械が語源です。ただ自動で動くだけでなく、問題が起きたときに機械を止める判断までできる機能を持つため、「自動」ではなく「自働」という言葉が使われたといいます。
現在の自動車生産工場でも、「自働化」は受け継がれています。生産工程のどこかに異常があった場合、機械は自らそれを「異常である」と判断して動きを止めるのです。これにより、不良品の生産が減る上、従業員1人で何台もの機械を稼働できるようになり生産効率も格段にアップします。
②ジャストインタイム
ジャストインタイムは「必要なものを、必要なときに、必要なだけ」つくる生産方法のこと。これも、トヨタ自動車が編み出した効率化の仕組みです。ジャストインタイムのおかげで、
- 無駄がなくなる
- 生産性が高まる
- 短時間で大量生産できる
- より少ないコストで生産できる
ことが可能になります。
かんばん方式とは?
「かんばん方式」もトヨタ自動車独自の生産管理方法で、「スーパーマーケット方式」ともいわれています。
スーパーマーケットなど多くの商品を扱う事業所では、商品名や品番などが記載されたカードを用いて商品が管理されているのです。この方法にヒントを得て生産管理の現場に、重要な情報を記載したカード(かんばん)を取り入れたことから「かんばん方式」と呼ばれるようになりました。
かんばん方式を応用した仕組みが、ジャストインタイムです。
- 必要な在庫を必要な量だけそろえるスーパーマーケットを生産の前工程
- 商品を買いに来る客を後工程
に見立てて、効率的なシステムとして組み立てられたのです。
2.ジャストインタイムの三原則
ジャストインタイムには、顧客の需要によって生産量や種類を平準化することに加え、3つの原則があります。
- 必要数によってラインタクトを決める
- 後工程の引取り(「かんばん方式」が使われる)
- 工程の流れ化
平準化生産とは?
生産の平準化とは生産量や種類、時間などを平均化すること。平準化することで、生産のバラつきや無駄をなくすことができます。反対に、生産量や時間などにバラつきが出てしまうと、ジャストインタイムからは遠ざかり、無駄が発生します。
ジャストインタイムには平準化が大前提なのです。
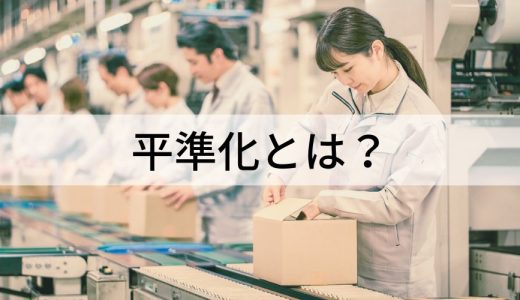
業務平準化とは? 意味や標準化との違い、進め方、事例を簡単に
平準化(へいじゅんか)とは、バラバラの物事を均一化して公平にすること。本記事では、平準化と標準化・平均化との違いや、業務平準化が重要な理由、業務平準化ができていない状態などについて解説します。
1....
①必要数によってラインタクトを決定する
三原則の1つ目は必要数に応じてラインタクト(=生産にかける時間)を決めるということ。
しかし、売れ行きによって生産しなければいけない数量は変動します。無駄を出さないためには、売れ行きに見合った生産をする必要があるでしょう。必要なものを必要な分だけ、必要なスピードで生産する仕組みをつくる必要があるのことです。
②後工程の引取り
2つ目の原則後工程の引取りは、かんばん方式を使った方法。
最終工程の段階で生産の計画を指示し、後工程で使った部品を、使った分だけ前工程に取りに行きます。前工程は後工程が持っていった分だけ生産すればよいため、分かりやすくなるのです。
販売数に合わせて生産できるこのシステムでは、トヨタで「かんばん」と呼ばれていたカードが使われます。
③工程を流れとする
3つ目の原則は、生産効率をさらにアップさせるための仕組みです。工程をスムーズに進めるため1つの製品の生産工程を1つの流れとしてつくります。
そうすることで、次に別の種類の製品をつくる際、設定の変更や生産ラインの切り替えがスムーズになるのです。
この生産工程の流れ化は、多くのスタッフを必要とする場合だけでなく、1人で管理できる工程においても同様に考えます。
ジャストインタイムの図解
ジャストインタイムが確立された当時の副社長氏は、スーパーマーケットの在庫管理をもとにした「かんばん方式」を採用しました。
図のように、後工程がAの部品を受け取り、前工程では渡してしまったAを補充生産する、という仕組みになっています。
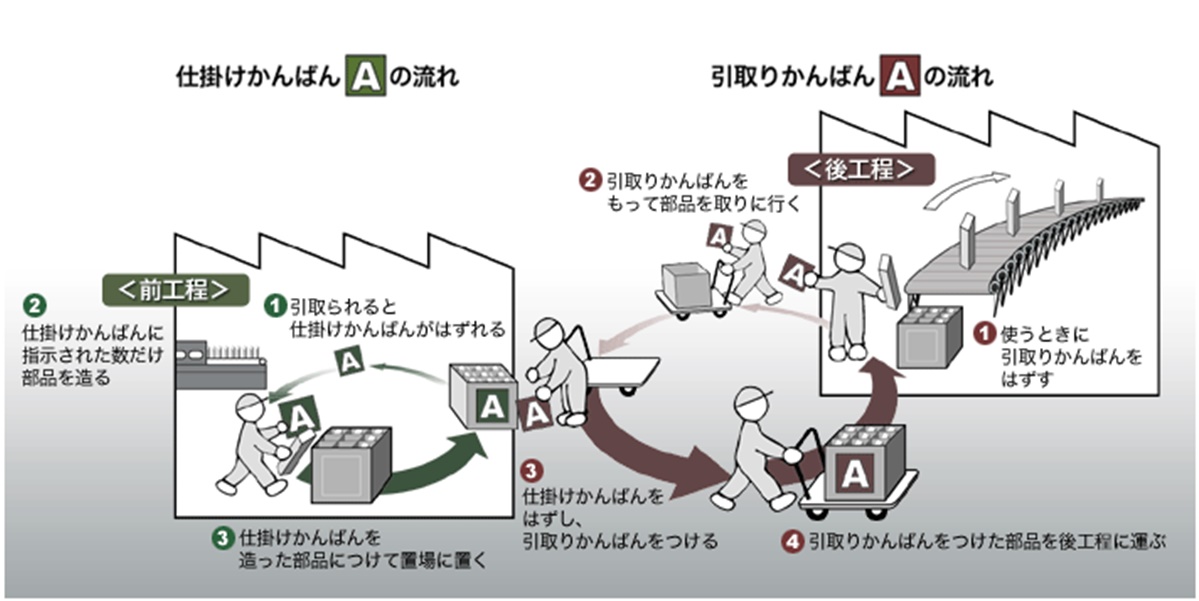
画像引用:TOYOTA「ジャスト・イン・タイムについて」https://www.toyota.co.jp/
3.ジャストインタイムの起源
ジャストインタイムの起源は、トヨタ自動車の実質的創業者である豊田喜一郎氏が提唱した生産方法にあります。彼は、挙母工場を稼働させる際、次のように語っていたそうです。
「無駄と過剰のない事。部分品が移動し循環してゆくに就いて『待たせたり』しない事。『ジャスト、インタイム』に各部分品が整えられる事が大切だと思います。」
挙母工場が完成する前から、彼は「ジャストインタイム」を口癖のように多用していたそうで、この信念は、第五代社長の豊田英二氏に引き継がれました。
発想の起源:豊田喜一郎
現在のトヨタ自動車のもとは、自動織機を使った織物工場にあります。自動車部品の製造を始めたのは昭和8年で、織物工場内に自動車製造工場を設けて製造していました。しかし、もともと自動車専用の工場ではなかったために、設備に限界がきてしまったのです。
その状況を打開するために建設された、自動車製造を目的とした工場が挙母工場です。
創業者・豊田喜一郎氏は、この挙母工場をつくるに当たり、必要なものを必要な分だけつくる「ジャストインタイム」を口癖のように唱えていたと伝わっています。
ジャストインタイム生産の中断
無駄を省く画期的な生産方法である「ジャストインタイム」を進めようとしていたトヨタ自動車でしたが、その斬新な発想が受け入れられるまでには時間がかかりました。加えて、戦況の悪化に伴って、物資を手に入れることが難しくなっていったのです。
1939年には、自動車生産用資材の割当配給制が施行。これにより必要に応じた種類や量を手に入れることができなくなってしまいました。これにより、ジャストインタイム生産は一時中断を余儀なくされたのです。
ジャストインタイムの実現(「スーパーマーケット」方式)
その後、ジャストインタイムが本格的に進められたのは、戦後になってから。1954年、後工程が前工程へ必要なものを必要な分だけ取りに行く「かんばん方式」が考案され、ここでやっと喜一郎氏が求めていた「ジャストインタイム」が現実のものとなったのです。
合理的で斬新な「ジャストインタイム」の考え方は当初、なかなか受け入れられませんでした。しかし、紆余曲折を経つつ、少しずつその効果が認識されるようになり、今では世界中で知られています。創業者である喜一郎氏の発想は、今も受け継がれているのです。
4.ジャストインタイムとBTOの違いは? 仕組みと具体例
毎日必要な分のみ生産するというジャストインタイムと似た発想の生産方法に、BTO(受注生産方式)というものがあります。
BTOとジャストインタイムにはどのような違いがあるのでしょうか。その仕組みと相違点を見ていきましょう。
BTO(受注生産方式)とは?
BTO(受注生産方式)とは顧客の希望に合わせた製品を、顧客の注文を受けてから製造する方法のこと。一方、ジャストインタイムは、BTOを行う上で問題となる在庫管理のリスクを減らすための仕組みです。
BTOで選べるオプションが多いと、それだけメーカー側はパーツの在庫を持たなくてはいけません。そこですべてのパーツを自社で在庫せず、必要なときに必要な分だけ準備する考え方としてジャストインタイムが導入されました。
BTO生産方式の具体例と利点【デル・モデル】
BTOの生産で有名なのは、コンピューターメーカーのDell(デル)が取り入れている直接販売とBTOを組み合わせた方法でしょう。
購入者はデルのポータルサイトに行き、手順に従ってメモリやプロセッサの種類や容量などの詳細を選びます。デルは受注すると、希望内容に沿って製品を製造し、直接顧客に送り届けます。
この方法はデル・モデルと呼ばれ、今まであらゆる企業が参考にしてきました。
BTOのデメリット
BTOは無駄のない合理的な生産方法に見えますが、デメリットもあります。顧客の要望に合わせたものを生産するため、パーツの管理が難しくなるのです。
ジャストインタイムの方式によって、自社で在庫するリスクはなくなりますが、受注があった場合、素早くパーツを確保しなくてはなりません。しかし、ある部品が在庫切れになっていると、納期にかなり時間がかかってしまいます。
そうした事情を踏まえてかデルの社長は、日本で行われた記者会見で、BTOでカスタマイズの注文を受けていた製品のスペックを固定するかたちに移行すると発表しました。
BTOについて解説しましたが、改めてジャストインタイムとの違いをまとめてみましょう。
品物や場所の無駄が出るというBTOのデメリットを解消できるのがジャストインタイム。自社で在庫せず、必要な際に必要な量だけ仕入れるため、時間やコストの無駄を減らすことが可能です。
つまり、BTOは販売から生産・納品に至るまでの方法、ジャストインタイムは生産するに当たっての管理方法を指します。
5.ジャストインタイムを導入したほうがよい企業・しないほうがよい企業
ジャストインタイムは、うまく導入すれば、無駄を省いて効率的な生産ができます。そのため、多くの製造関係の企業がトヨタ自動車の手法を参考にしているのです。しかし、ジャストインタイムはすべての企業に有効な方式ではありません。
ルーチンの少ない製造ラインや人の手がほぼ入らないような製造ラインの場合、この方式は効果的ではないのです。また、
- 季節によって生産量が大きく変化する製品
- 医療機器など人命に直接関わる製品
などは、ジャストインタイムの管理の限界を超えてしまいます。
ジャストインタイムの目的
ジャストインタイムの目的には、以下の3つがあります。
- 生産性を高める
- リードタイムを短縮する
- 売れるタイミングで生産する
①生産性を高める
ジャストインタイムで期待されることは生産性の向上です。しかし導入によって生産性が直接的にアップするわけではありません。ジャストインタイムを取り入れて生産性が高い状態を維持できる体質に改善することが本質なのです。
導入したにも関わらず、なかなか効果が現れない場合、まず生産体制が改善されているかを見直しましょう。
②リードタイムを短縮する
リードタイム短縮の効果は、ジャストインタイムによって最も顕著に表れる部分です。リードタイムが短縮されることで、在庫を少なくできます。
さらに、作業工程の中で製造から検査までのリードタイムも短くなるため、ミスがあった場合早い段階で気付くことができます。それは、不良品を減らす・無駄な労働をなくすことにつながるでしょう。
何より、需要に見合った供給が可能になります。リードタイムが短ければ、需要がある分だけ生産できるため、結果欠品や廃棄といった無駄がなくなるのです。
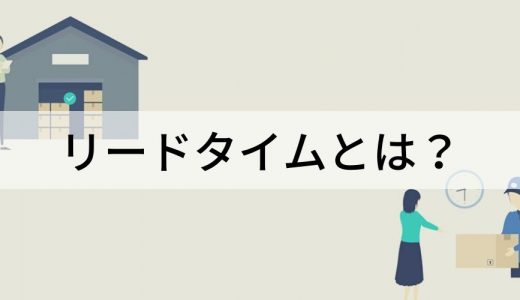
リードタイム/lead timeとは?【意味をわかりやすく】計算方法
リードタイムとは、スタートからゴールまでに要した時間のこと。ここでは、リードタイムについて解説します。
1.リードタイム(lead time)とは?
リードタイム(lead time)とは、あるプロ...
③売れるタイミングで生産する
在庫なし方式といわれるジャストインタイムのもう一つの効果が顧客を待たせることが減る点。
注文が入ってから生産、納品と進む流れがスムーズになるため、顧客を待たせることなく製品を届けることができます。結果、顧客満足度が高まり、企業イメージも向上するという相乗効果が生まれるのです。
また、売れるタイミングで製造するため、不要な生産がなくなり、コストや時間、場所、人にも余裕が生まれ、生産量もアップするでしょう。
ジャストインタイム導入の必要性があるメーカーとは?
ジャストインタイムが向いていないのは、
- ルーチンの少ない「受注設計製造スタイル」
- ほとんどの工程を機械のみで行う「装置産業スタイル」
などです。
反対に、これらに該当しない生産スタイルの企業では、ジャストインタイムの効果が得られるとされています。相性が良いはずの生産スタイルであるにも関わらず、効果が現れない場合、品質改善が必要なことも。
- 不良品率が10%以上
- 歩留まり率が90%未満
といった場合は、ロスの大きさがジャストインタイムの効果を上回ってしまっている可能性があります。
評価業務の「めんどうくさい」「時間がかかる」を一気に解決!
人事評価を効率的に行うための活用方法が満載! カオナビの資料ダウンロードはこちら
◆資料内容抜粋 (全31ページ)
・人事評価システム「カオナビ」とは?
・人事のお悩み別 活用事例9選
・専任サポートについて など